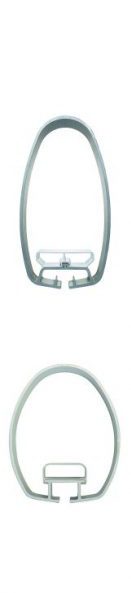
Every Seldén rig is carefully thought out, down to the last detail.
All the way from the materials and functions of the different parts of the rig, to dimensioning the right rig for each individual boat. Each component contributes to the performance of the whole rig. That is the Seldén way – experienced yachtsmen behind every aspect of design, product development and production.
Since 1992 we have engraved a unique code into the mast section. We call it the mast ID number and you find it at the lower end of the aluminium section. This number tells us when your mast was built and what parts were used all the way down to nuts and bolts. The mast ID number includes the designation of your mast section which enables you to find part numbers in our catalogues and sparepart lists, all to be found under Technical Support.
A corresponding number is to be found in the forward lower end of your boom. Best of all – take a close look at the components on your mast and you will find part numbers on them. Can it be simpler? Complete rigs and spareparts are sold by our World wide network of independent rigging companies.
Our conventional masts for 26-80 feet yachts are divided in two categories. The longitudinal oriented sections and the lateral oriented. Which one we select depends on the chain plate locations of the boat and number of spreaders.
These sections are used for rig configurations with in-line spreaders or moderate spreader angles. The relationship between the length / width is 1,9 in order to create longitudinal stiffness allowing higher forestay load tensioning the backstay. Running backstays can often be avoided and the risk of mast pumping is also reduced. These rigs normally come with multiple pairs of spreaders and they are designed for the popular MDS sliders (Multi Directional Support).
For rigs with large spreader angles, lateral stiffness is of higher importance than longitudinal stiffness. This is the result of a large spreader angle creating longitudinal stability, whereas the lateral stability is achieved by the geometry of the mast section. This makes for a mast section which is wider and rounder than the corresponding longitudinal section and therefore the number of spreaders can be reduced. These sections are popular for upgrading a boat from the 1970-90’s with a traditional style single spreader rig, but still with all the benefits of modern functions such as the Inner Wheel Sliders (IWS).
Seldén’s seven aluminium keelboat sections feature a wealth of sophisticated and functional solutions, originating from the dinghy range and the yacht range. The sections are extruded and anodized and they are all available with a tapered top as an option. Let us design your keelboat rig or ask us for our One-design solutions.
Its unique features for reducing friction and initial sail resistance make furling and reefing child’s play. And it also makes sailing safer and far easier for you and your crew.
With a powered furling mast and a powered Furlex jib furler it is even easier to set, reef and handle your sails. You can work your sails single handed, without leaving the helm. Powered systems are available for yachts ranging from 35 to 70 feet.
Due to the easy handling, with a furling mast you will do more sailing and less motoring.
A Seldén furling mast makes it easy to unroll and set your mainsail. Rolling it in is just as quick and easy. As your sail is neatly stowed out of the way the instant it is rolled in, you have a clear view when manoeuvring under power.
You can set your sail to suit the weather conditions, from the safety of the cockpit.
By furling the sail vertically into the mast, you don’t have to furl very much to get a substantial decrease of the sail area.
You hoist the sail just once a season, so a small crew can manage a much larger boat.
There are no fixed reef points, so the number of combinations between furling genoa and main are unlimited.
The wide sail slot allows for vertical battens and a positive roach of the main sail and the sailgroove on the luff extrusion is located asymmetrically to help the sail furl easily around the extrusion.
The furling system is based on Seldén’s proven technology. Geared line driver winch, tensioned luff extrusion and the patented load distributor of the halyard swivel. All to make furling an easy and fast operation. The Seldén furling masts come with twin cable conduits, enabling the cables to run freely and well protected from all running rigging. The cable conduits also facilitate cable replacement.
There is an outhaul line for rolling out the sail, and an endless line for rolling it in. It’s simple as it sounds. Or if you wish, you can operate the sail at the mast using a winch handle. The geared reefing winch mechanism runs on ball bearings, so it takes little effort to roll in the sail. Greasing holes in the mast facilitate maintenance.
Two oval holes on the port side of the mast allow for easy access to the tack attachment, sail fees, tensioning screw and halyard swivel. Just remove the composite covers and the rest speaks for itself. You can inspect the halyard swivel and carry out annual maintenance through the upper access hole.
The outhaul cars are fitted with horizontal and vertical wheels, enabling them to absorb forces from every direction.
Turning blocks at the base of the mast are designed to enable the ready-spliced, endless line to be easily threaded into position. Seldén deck blocks have the same feature.
The sail groove on the luff extrusion is located asymmetrically to help the sail furl easily around the extrusion. In addition, the rotating luff extrusion is tensioned and fitted with ball bearings top and bottom. This reduces friction between the sail and the inside of the sail compartment.
To make sail handling easier for a small crew we have synchronized an electric motor in the mast with a newly developed electric winch for the outhaul, E40i. Push a button and the sail comes out in a controlled fashion as the winch adjusts the outhaul tension in relation to the motor in the mast. This is what we call Synchronized Main Furling.
Converting a manually operated furling mast is quite easy. Basically, the vertical shaft in the original line driver is replaced for a longer version which is connected to the motor. A clutch allows the motor to be disconnected for manual operation, if ever needed. The motor is completely integrated in the mast and connected to the Seldén Power Supply and SEL-Bus system.
The motor can be retrofitted to Seldén furling masts type RB (~36-43’ yachts).
See video:
How to upgrade a furling mast to electric drive
Push the ”OUT” button and the sail will start to unfurl. The E40i winch will tension up the outhaul while the mast motor feeds out the sail. The speed is increased when the ”IN” button is pushed in addition to ”OUT”. To reef, just release the outhaul from the winch and push ”IN”.
The E40i winch is built up around an electric motor which is totally integrated in the drum. Only three thin cables are protruding to lead through the coach roof or the deck, no large cutouts and no external motor or gearbox. This makes for uncompromised headroom down below which is normally not the case with electric winches.
The three speed operation provides a high speed gear, a moderate gear and a low speed gear for fine tuning. It is a two finger operation to start the winch and to swich gear, so a single-handed sailor can helm while adjusting the trim.
Carbon composite combines stiffness and strength with low weight. Seldén low-weight carbon spars have accentuated longitudinal stiffness. This means that forestay tension can be substantially increased. All experienced racing sailors know what this means in terms of increased upwind performance. The combination of greater stiffness and reduced weight will bring you beyond the speed limits.
Our carbon spars are designed using the latest finite element analysis backed by many years of solid engineering experience.
Our unique production method gives a unique look. We call it Mandrel Filament Moulding (MFM). The process is fully automated and computer controlled for ultimate accuracy, repeatability, efficiency and that stunning ‘Viper’ pattern.
Seldén produce over 400 carbon masts per year as well as booms, poles and bow sprits for boats including high performance skiffs, racing keelboats, IRC race boats and some of the world’s most prestigious cruising yachts. With more sailors choosing Seldén carbon spars, the pattern is obvious.
Working hand-in-hand with the world’s top dinghy sailors, carefully analysing their input and feedback, enables us to produce the ultimate Seldén dinghy rig for every boat. Ever since Seldén acquired Proctor in 1997, we have improved and developed the already acknowledged excellence of the Proctor products, so that they are now, like all other Seldén products, the best of the best. Our innovative design, attention to detail, advanced testing and manufacturing have won Seldén the trust of dinghy sailors all over the world and has contributed to numerous Championship medals.
Seldén has the design expertise and software to enable us to create a mast to meet exacting performance requirements. During the design process the position and alignment of each fibre is precisely calculated so as to meet the required bend characteristics. This detailed design is then used to program and control our filament winding equipment.
The combination of meticulous care, long experience, and exact specifications enable us to achieve optimum performance for minimum weight.
Computer controlled laminate lay-up Carbon filaments are wound around a mandrel (male mould), under controlled tension, via a designated winding program supplied by the design team.
FILAMENT WINDING, a computer-controlled process (CNC), guarantees consistent and accurate filament fibre orientation from spar to spar. Carbon filaments can be laid from 0° (uni-directional) to leave 89° (hoops) and at all angles between to produce a wide range of bend characteristic requirements. This accurate alignment of composite filaments is vital to the performance characteristics of a carbon spar. Fibres are laid under tension, which means that we can make the most efficient material choice and supply the lightest spars on the market.
This process gives a Seldén spar a level of tube consistency unattainable via any other composite manufacturing technique. Hence, the mast you buy will perform as well for you as it will for a world champion sailor!
Only the highest grade pre-preg tows of T700 or TZ carbon fibre are used to give sailors the best stiffness-to-weight spar. This, in combination with our filament winding process, enables the highest fibre-to-resin content pre-preg to be used.
The aerospace grade pre-preg has a UV stabiliser in the resin system to give the spars a guaranteed long life, even in the sunniest of climates. More fibres and less resin, mean lighter, stiffer masts.
The consolidation of the material to form a ready-to-assemble carbon tube is completed in our in-house 20-metre long autoclave. The combination of heat and pressure to cure the resin and consolidate the pre-preg material ensures a strong and consistent final product.